Wire. Our primary material.
We mainly process round wires made of steel and stainless steel in the diameter range Ø2.0 to Ø10.0 mm. However, flat wires with rectangular or square cross-sections are also used in our company. We even weld profiles, sheets or 3-dimensional (wire) bent parts in-house to form wire mesh constructions or entire component groups. Every year, we produce a total of approx. 6,500 to. of primary material (roughly equivalent to a lorry load of 25 tonnes per day) that we form in this way in Wegberg for the European market.
Round or flat wire is always "drawn" from wire rod, i.e. formed without cutting using tension and pressure. As an original mass product, steel is first obtained from iron ore in the electric steel process by melting scrap or in a blast furnace, in each case with the addition of the corresponding alloying elements. The cast slabs or billets are then rolled out into wire rod - seemingly endless, coiled in a ring shape, covered with scale as it cools and, as it is only rolled by means of circumferentially arranged rollers, not really round. Only in a wire drawing mill does wire become the manufacturing wire that we use today. If round, smooth wire is required, the material is usually drawn through one (or more tapered) drawing dies using cold forming. If roundness is not so important, or if the wire is to be given a surface profile (reinforcing steel), for example, roller rollers in so-called drawing cassettes are used as an alternative. Corresponding DIN EN standards regulate the most important aspects of outer diameter, roundness or surface quality. The chemical composition of the (rolled) wire is also important, as this determines, for example, weldability, strength and elongation, galvanisability, etc.
Incidentally, the thinnest wire rod produced today measures 5.5 mm in diameter. This means that the subsequent drawing process, which inevitably leads to a hardening of the material by reducing the outer diameter, reaches its technological limits: the thinner, the harder. From approx. Ø2.5 - 2.0 mm, normal steel wire reaches a degree of hardness that makes a further reduction in diameter impossible - intermediate annealing is then unavoidable. Depending on the final diameter of the desired wire (think, for example, of medical technology and its so-called micro wires with diameters of a few µm), the drawing and annealing processes alternate many times during production.
The surface of the iron wires used at K&L is not always bright, or "bright bright" to be more accurate. Wire drawing plants also supply "bright", "dry bright" or "wet bright" grades, for example, depending on which drawing agent (soap, grease, oil, etc.) is used and/or which post-processing of the surface (rinsed, brushed, blasted, etc.) is carried out at the end of the drawing process. The "correct" surface of the bare wire always depends on the subsequent processing method or intended use of the end product.
For example, the requirement for minimum surface roughness is very high if chrome plating is to be carried out afterwards - in contrast, the macrostructure of the surface hardly plays a role if the wires or (mesh) end products are subsequently hot-dip galvanised.
In many cases, the wire, which is always iron wire of grade St-37 or St-52 at its core, is also "refined" during the drawing process. For example, through galvanic copper plating or galvanising. The latter can also be carried out electrolytically (electroplating) or classically - and almost without exception in mass production - as hot-dip galvanising in a continuous process. But be careful: The supplier or customer must clearly define the type and method in advance, as the end product is generally only referred to as "pre-galvanised wire". A distinction is made here in terms of strength and elongation ("hard" or "soft galvanised") and the thickness of the zinc coating (e.g. "normal" = approx. 80gr/m2 or "thick galvanised" = approx. 350gr/m2). Finally, in the truest sense of the word, there is also the delivery form "galvanised redrawn" to homogenise the surface, i.e. the wire is reduced to its final nominal diameter by a subsequent drawing process after hot-dip galvanising.
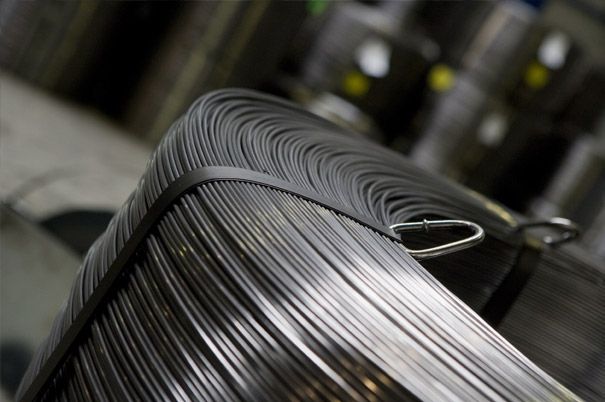



Another important way of differentiating pre-galvanised wire is the chemical composition of the applied zinc coating. In addition to normal zinc, a special alloy of zinc-aluminium ("Galfan") has proven its worth here for several years now. The aluminium content here is up to 5% and ensures that zinc can flow back to the spot weld and protect against corrosion when the wires are subsequently welded. Another effect of this alloy as such, which is controversially discussed in the relevant literature, is the electrolytic effect of this alloy on the environment. A kind of ion sheath, as one should imagine, then completely surrounds the wire surface and prevents the hydrogen particles from the air from forming a rusty bond with the iron bound in the wire. However you imagine this perpetual battle between the ions on the surface of the wire to be protected, this zinc-aluminium alloyed wire has in fact found its (ge)important role in the wide world of wire products today. Gabions (gravel baskets), shelves for poultry farms and increasingly also fence elements are made from such Galfan wire.
We get it done. Together.
Contact
Phone: +49 (0)2432 9889 - 0
Fax: +49 (0)2432 9889 - 48
E-Mail:
Web: www.schweissgitter.de